TOPIC: ELKINS FARMS
Type of service
Academic paper writing
Type of assignment
Case study
Subject
Management
Pages / words
4 / 1100
Academic level
Junior (College 3rd year)
Paper format
Line spacing
Double
Language style
US English
You saw most stuffs were taken from the doc I sent to you
I want the writer to revise it and make sure it doesn’t reflect what’s on the doc I sent to you, which is the instructo’s material
And remind the writer
To answer it as a question and answer
Not to draft it all like an essay.
16:55
Question 1 and answer
Question 2 and answer
Till question 5
case study:
Overview
Elkins Farms has been a leading producer of dairy products for the southeastern region of Idaho since 1942. It is the second largest of the 600 dairy farms in Idaho, a state which has the fourth highest number of dairy farms in the United States, surpassed only by California, Wisconsin and New York. Like in other states across the country, Idaho dairy farms are declining in number for economic reasons. Dairy product prices in the U.S. have dropped dramatically during the past four years because the industry’s production capacity has met demand nationally and internationally. A strong dollar also makes it difficult for foreign consumers to afford U.S. dairy exports. Fewer exports and the money associated with them have forced many U.S. farms to sell off their operations to competitors. Luckily for Elkins Farms, only about 3 percent of its dairy production is exported outside the U.S.
Elkins Farms has had a long-term strategy for more than 20 years to become larger and more productive. Elkins Farms bought three adjoining farms between 1995 and 2005, expanding its holdings to its current 3,000 acres. Family-owned and operated for four generations, Elkins Farms began with a herd of 15 cows and 225 chickens on roughly 100 acres of land five miles west of the town of Idaho Falls, Idaho. Today, Elkins Farms is home to 2,000 cows and 3.5 million chickens.
The latest expansion required the farm to hire workers at a faster rate than ever before. The number of employees in its production facilities increased more than 125 percent during that 10-year period. As the farm continued to add new employees, it also began investing in technology to become more efficient in its rapidly growing dairy and egg production facilities. Elkins Farms currently employs 245 full-time and 140 seasonal employees. Thirty- five percent of the workforce are immigrants, the majority of whom originate from Mexico, Guatemala and Nicaragua. Dairy farms that hire immigrant laborers are often vilified because people feel they are taking away jobs from U.S. citizens. Elkins Farms, like many in a similar position, is quick to defend its hiring practices. In a recent interview with a local television station, Elkins Farms CEO Michael Alexander said, “I don’t know if we could exist without our immigrant workers. They are hardworking, dependable and willing to learn. We have hired local resident who have been exceptional workers. To be frank, though, there aren’t a lot of them lining up for work.” With a smile, he added, “It’s not easy work. Let’s just say the conditions are less than ideal for most, and we can’t have everyone working the 9-to-5 shift. Cows can’t milk themselves.”
Elkins Farms knows that despite its strong position in the market, it needs to adapt to changing conditions to be successful in the long term. The farm currently has state-of-the-art processing and production plants for its milk and egg operations. Two of the three dairy production facilities have already reached capacity, and the third is expected to be at capacity within the next two years. The farm recently broke ground on a fourth facility, which will be completed in nine months. Elkins also recently redesigned its manufacturing plant to increase production because of demand for other beverages it makes, including iced tea, lemonade and fruit drinks. Elkins Farms is a top supplier to major supermarket chains in Idaho, Wyoming, Montana and Utah, providing supermarkets with its full beverage line and egg products.
Elkins Farms opened its first restaurant in 1997 next to its headquarters, with a second restaurant opening in 2006 just 10 miles north of Idaho Falls. A visitor center was added in 1998 and has grown significantly over the years to include a gift shop. The center also hosts farm tours throughout the year to thousands of guests. Elkins Farms believes its strategic diversification over the past 20 years has helped it navigate market fluctuations caused by the economy and extreme weather conditions.
FOURTH-GENERATION FAMILY FARMING
Elkins Farms CEO Michael Alexander spent the majority of his childhood on the farm. His father and grandfather often talked about how interested Michael became in farming at an early age, peppering them with questions about different areas of the operation. Michael earned his bachelor’s degree in business administration from the University of Idaho. He spent the next 15 years after graduation overseeing every operation at Elkins Farms, with exception of the restaurant. He was promoted to general manager in 1998 and served in that capacity under his father’s guidance until his father’s retirement in 2005. Michael met his wife, Suzanne, at the University of Idaho. Suzanne has since pursued her passion in marketing and communications to build and oversee Elkin’s marketing department. It was Suzanne’s vision that led to the creation of the visitor center, which attracts multiple generations to Elkins Farms. Michael and Suzanne have three children. Bryce is their oldest and has been the general manager of Elkins Farms for the past eight years. He has a background in logistics and supply chain management. Before his current role, Bryce oversaw the shipping and receiving department for four years. Michael and Suzanne’s oldest daughter, Jan, has been the director of finance for the past four years. She joined Elkins Farms after college and worked as an accounting clerk and budget manager for the farm for six years before assuming her current role.
Sara is the youngest of the three. Unlike her siblings, she did not have a direct path to Elkins Farms. Sara, known by her parents as the “free spirit” of the family, decided that she wanted to create her own opportunities and not rely on her family to get her a job at Elkins Farms. Sara studied to be a secondary education teacher at the University of Idaho but realized during her student teaching experience that teaching was not the career for her. After graduation she accepted a position as a human resource specialist for a Fortune 500 global food supplier. After three years in that role, she took a job as an organizational development consultant for another Fortune 500 company. Her specialty was organizational change initiatives, including corporate restructuring. Michael has always been concerned about how his family is perceived by his employees and the public. He doesn’t want employees to think his children were handed management positions. He made it clear to Bryce and Jan when they joined the business that they would have to learn the entire operation from the ground up. Both started by milking cows and caring for the chickens.
THE BRIEF UNSUCCESSFUL HISTORY OF HUMAN RESOURCES AT ELKINS FARMS
The human resource (HR) department at Elkins Farms consists of three full-time employees—an HR manager, an HR coordinator and a payroll clerk—and a part-time HR assistant. The organization hired its first HR professional in 1998 when it added its retail operation. As the organization grew and diversified, the management team realized it needed to formalize its HR systems. Michael felt that the complexities of running the farm required managers to become less hands-on and to think more strategically; he also believed that laborers should become more specialized. This was Michael’s ideal scenario, but the reality was far from ideal. Despite an intentional shift to formalize HR, all of the divisions—including the production facilities— continued to operate as they did before. Encouraging managers to think and operate more strategically continues to be a challenge. For example, Michael has expressed his frustration to Bryce that production supervisors are not taking full advantage of the additional data being gathered through recent technological advances to support the farm’s long-term growth. They also lack core supervisory skills to motivate employees to perform their best.
Recruiting and retaining employees with the appropriate skills continues to be a challenge. Many production employees join Elkins without any previous farming experience. There is also significant employee turnover in the production facilities, primarily in the nonimmigrant labor force. And the lack of advancement opportunities frustrates employees. Although HR programs like onboarding and professional development are becoming formalized, managers are not consistent in enforcing HR policies with their staff. In addition, establishing performance goals, performance evaluation systems, effective recruiting and employee training have had limited success. Employee turnover has increased nearly 25 percent during the past five years, and managers are beginning to realize that practices need to change to become more productive in the long run.
Michael understands that the farm’s past investment in HR has not provided the results he wanted to achieve. He has contemplated for several days about calling his youngest daughter, who he knew would be able to build the HR systems Elkins required. Michael has been hesitant to call Sara because he knew she wanted to create her own future. He also knew how fulfilling her career had been; all he ever wanted was to see his children happy in their chosen profession. Elkins Farms was experiencing a series of workforce challenges, however, including recruiting and cross-cultural communication. These challenges led to the departure of their second HR manager in five years and the third in 10 years. The last two managers cited “relocation” as the reason for leaving, but Michael knew the fit had not been ideal in both instances. Both had sound HR backgrounds but lacked the strategic perspective Elkins Farms desperately needed. Cultural issues at Elkins Farms—mainly resistance to formal HR policies and procedures—also have contributed to the lack of progress. Michael wondered how much of this failure was due to his own lack of appreciation for the HR function. He certainly was not proud that the HR manager position had turned over three times in a 10-year period.
It is never easy to revise policies and procedures in a change-resistant culture like Elkins Farms. Did he want his own daughter to experience those challenges? Whatever he decided, he knew he needed to get it right this time. Despite a lack of HR systems, Elkins had been successful, but Michael knew advancing HR was critical to maintaining and growing Elkins Farms in the long term.
Michael held a series of conversations with Sara and finally convinced her to join the family organization. The last conversation took place over a holiday weekend when Sara was visiting her family. Michael and Sara walked around the farm after dinner one night and discussed several topics. When Sara asked if she would be reporting to her sister, Jan (director of finance), Michael laughed to deflect the awkwardness of the moment. Sara took this as a “yes.”
The previous HR managers reported to the director of finance, the last two reporting to Jan. Sara stopped and turned to her father, “You’ve gone through three HR managers in 10 years. I don’t want any special treatment, and I mean no disrespect to Jan. But if you want to have a strong HR operation and one that is finally respected, I need to report to you.” Michael hesitated briefly and said, “I need to talk with your sister, but I think it will be a welcome relief for her. She would be the first to admit that she didn’t give HR the support it needed. It will be a director-level position, titled director of human resources since you’ll be reporting directly to me.” Sara Alexander became the newest employee of Elkins Farms two months later.
Figure 1: Organizational Structure: Elkins Farms
Chief Executive Officer
Michael Alexander
Director of Sales
Scott Tobias
Director of Marketing & Community Relations Lillian McGinty
Director of IT
Vic Reston
Director of Operations Bryce Alexander
Director of Finance Jan Phillips
Director of HR
Sara Alexander
Idaho
Marketing
Enterprise Systems
Diary Production
Controller
Human Resources
Wyoming
Communications
Infrastructure
Egg Production
Budget
Payroll
Montana
Community Relations
Bottling
Accounts Payable/ Accounts Receivable
Utah
Retail and Visitor Center
Maintenance
Sustainability
Figure 2: HR Organizational Structure of Elkins Farms
Figure 3: Number of Employees by Department
Department Full-Time Part-Time/Seasonal | ||
Dairy Production | 47 | 23 |
Egg Production | 29 | 12 |
Bottling Production | 22 | 10 |
Retail and Visitor Center | 14 | 36 |
Restaurant Operation | 37 | 35 |
Maintenance | 24 | 8 |
Sustainability | 8 | 1 |
Administration (marketing, communications, IT, HR, finance, sales, senior management | 64 | 15 |
Total Employees | 245 | 140 |
HR Technology/ Fair Labor Standards Act (FLSA)
Elkins Farms has focused extensively on becoming a more sustainable operation for financial and environmental reasons. The farm is now equipped with 3,300 solar panels that generate 1.2 million kilowatts of clean, renewable energy every year. Elkins Farms has invested more than $6.5 million over the past five years into its dairy and egg production operations. The implementation of new technology has allowed Elkins to make better business decisions while increasing overall production. Elkin’s business strategy, like many other large farms, is to increase the economies of scale to allow for greater efficiencies, because to survive, the farm must increase the volume in its production facilities.
Precision Dairy Farming
The technology in dairy farming, known as precision dairy farming, helps Elkins measure the physiological and behavioral well-being of its herd and its overall productivity. In keeping with its reputation of providing excellent care to its animals, Elkins Farms was one of the first farms in the country to install an automated heating ventilation air conditioning (HVAC) system that will automatically kick on when outside conditions reach a certain temperature. It also has installed new stainless-steel Herringbone milking parlors, each priced at $750,000. The parlors are safer for the cows and better utilize space.
Many smaller farms are transitioning to automated milking systems that use robotic technology to manage the production process. Elkins, given the size of its herd, decided not to follow the trend, citing that it was not cost effective. With the change to the new parlors, all cows are equipped with enhanced automatic metering systems with individual tracking capabilities. These pedometers are placed on the cow’s ankle and monitor several pieces of critical data to help manage production. Before the pedometers, the data gathered were limited to the number of pounds of milk each cow delivered per parlor visit/day and the length of time each cow was in the parlor.
With the new parlors and software, farm managers can collect other data, including the amount of feed consumed per cow and the exact location of each cow using GPS. From a health perspective, the data allow for early detection of potential problems, including lameness, mastitis, infertility or other diseases. To support this effort, video cameras have been installed at the new milking parlors to identify any abnormalities in cows’ behavior as they leave the milking area. Cows are now milked three times each day (an increase from two), which not only is highly productive but decreases the less chance of infection. All of the information generated is now available through the use of tablets that provide “real time” data.
Elkins recently installed an automated manure removal system that cleans waste as cows are directed into the milking parlor. In addition to creating a better working environment, the system moves the manure so it can be used as fertilizer across the farm. In addition, Elkins recently received a grant through the state’s environmental protection agency to partner with a biotech company to significantly reduce the amount of runoff created by animal waste. Approximately 70 percent of the nitrogen and phosphorus in cow waste is collected and used as fertilizer.
Automation in Egg Production
The egg production operation has also experienced a series of transformations in the past several years, including the opening of a new state-of-the-art production facility last year. Unlike the dairy operation, Elkins automated most of its egg production. The egg production facility is equipped with tunnel air conditioning and a waste disposal system that transports the waste from below the chicken cages. The waste is then used as fertilizer.
The average chicken lays one egg a day; some produce more, and some less. Egg production depends on several factors, including the breed and age of the chicken, the time of year, and the environmental conditions in the egg facility. Production at Elkins Farms once averaged one egg every two days. Now, the 3.5 million chickens at Elkins Farms produce an average of 115,000 eggs per hour, or approximately 2.75 million eggs per day.
Elkins Farms believes that the recent change to larger cages has a lot to do with the increase in productivity. A spokesperson was recently quoted in a national publication as saying, “Roomier cages result in less stressful and more productive birds.” Approximately 97 percent of the Elkins Farms’ eggs are rated AA Quality, the highest quality rating. The improvements in efficiency have resulted in eggs being transported from the facility roughly three hours after being laid. Elkins Farms is recognized as having the highest quality control levels in the business.
Challenges in Workforce Planning
The rapid introduction of technology into the dairy and egg production facilities has not been without its set of challenges. Many dairy employees are frustrated with the level of customer service they have received from their milking parlor vendor. When the milking parlors were installed, for example, Elkins employees felt the training they received was insufficient. The training was not only brief but limited in terms of the number of employees who could attend. Only supervisors and selected long-tenured employees participated in the training. As one supervisor said, “They trained a few of us and expected us to train the rest of our employees. You can tell they put their resources into the technology and not their support.” Those who were trained have spent the majority of their time trying to understand the new technology and troubleshooting issues as they arise. To date, the HR department has had limited involvement in the implementation of the technology in the milking parlors.
Elkins is also struggling to realize a significant return on investment following multiple phases of technology upgrades to its production facilities. Despite the increased output of eggs through the automation, managers have seen an increase in overall labor costs. The operation that was once labor-intensive is now highly automated and includes washing, sorting and packing the eggs. Because of Elkin’s quality standards, however, other areas continue to require labor. This includes candling (examining the quality of the eggs for consumption) and shipping. These positions require certifications and, in some instances, advanced degrees. Sara Alexander, director of human resources, has argued since her arrival to the organization that much of the increased labor costs can be attributed to the lack of HR planning when the production facility was being constructed. The new operation requires less labor overall but more technical proficiency for those who work at the facility. Elkins has repositioned some of its employees to the dairy and feed operation as openings become available, but supervisors realize they need to reduce labor costs to reach optimal efficiencies.
Bryce Alexander, director of operations, told Sara of the ongoing issues that the technological enhancements created in managing the workforce, but she still has several questions that need to be answered. As she was learning about the inefficiencies in the dairy and egg operations, she was also faced with a related challenge of addressing the classification status of all Elkins employees. Silvia Blair has been the HR coordinator at Elkins Farms for the past three years after graduating from a local community college with a degree in business administration. Sara’s assessment of Silvia has been mainly positive, recognizing her strong work ethic and willingness to learn. However, Sara also realizes that Silvia lacks proficiency in the compliance side of human resources. In fact, Sara feels Silvia’s strengths are in the transactional side of HR and wants her to “step back” to see the operations from a more holistic perspective. Silvia acknowledged to Sara her tendency to work at a fast pace to “cross it off her list” while moving on to the next challenge. Sara recalls a comment Silvia made in their first sit-down meeting, “I notice I become bored if I work on a task for too long.” Hearing this, it didn’t surprise Sara to hear that Silvia managed to complete the job descriptions for every position at Elkins Farms before Sara’s arrival.
Although Sara was pleased to see the work completed, she still questioned if the actual duties were captured to reflect the technology upgrades to the facilities. This then led to her concern about the exemption status of many of the production employees. Several of the laborers were classified as exempt based solely on the current salary test of $23,660 annually, despite their primary duties not reflecting such a classification. In addition, Sara wasn’t sure how many hours each of the employees in question worked during a given week, but she was convinced it was well beyond the 40-hour overtime eligibility threshold set by the Department of Labor. Knowing HR was not going to figure this out alone, Sara decided to meet with Bryce to determine how her department can gather an accurate assessment of the production positions to better understand the challenges that lie ahead for Elkins Farms.
In Bryce’s Office
Bryce was busy finishing an e-mail when Sara arrived at his office. Without looking away from his screen, Bryce motioned Sara into his office, apologizing for having to complete his current task before the meeting began. When he finished, he joined Sara at the conference table in his office, bringing his lukewarm cup of coffee with him.
It was apparent to Sara that Bryce’s mind was focused on issues outside of this meeting. Although Sara called for the meeting, Bryce set the tone of the meeting by stating with some degree of frustration, “Before we start, can I ask why we are talking about job descriptions again? My staff and I already spent a lot of time with Silvia. I thought this was completed.” Growing up, Sara never backed down from her older brother, and she wasn’t about to start in this meeting. However, she also knew that she wasn’t going to place her department in a positive light by arguing with Bryce. Sara acknowledged her brother’s frustration. “I know this has already required a significant amount of your team’s time,” she began. She then added, “But my main concern is that the technology upgrades were not captured in all instances. In fact, Silvia told me that she received some job descriptions back from supervisors marked as approved but without any changes made. I doubt they even reviewed them before sending them to us.” She paused slightly to gauge how Bryce would respond. Hearing no objections thus far, she continued, “Look, I’m frustrated it wasn’t completed correctly in the first place, but I know in several instances the technology upgrades have not been added to the job descriptions. This will definitely affect how positions are classified.” She added, “Bryce, I know Silvia was not given the access needed to conduct a thorough job analysis.” This last statement invoked a response. “Analysis! I’m not sure what you are referring to, but I know when anyone uses that term with me, it usually means a lot more of my time.” In attempts to reason with his sister as well as push toward a conclusion to the meeting, Bryce added, “I’m sure there are a thousand things HR can be doing right now. Why does this have to be at the top of the list?”
CASE STUDY QUESTIONS
1. What is HR’s role in addressing the workplace planning issues facing Elkins Farms?
2. What criteria must HR use to determine employee classification at Elkins Farms?
3. Assuming many of the production positions will need to be reclassified, what are the employee relations challenges HR faces when informing employees who will be affected by such a change? What are the most important points to communicate to the farm employees?
4. In referring to Sara’s recommendation to conduct a job analysis, Bryce responded, “I’m sure there are a thousand things HR can be doing right now. Why does this have to be at the top of the list?” Placing yourself in the role of Sara, would you agree that conducting a job analysis is a priority for human resources and the organization? Explain your response. If you were Sara, how would you recommend conducting the job analysis?
5. Draft the following letters, paying particular attention to the tone of the communication and how it will be received:
a. A letter to an employee whose position has been reclassified to nonexempt and whose pay will remain at $43,500.
b. A letter to an employee whose position has been reclassified as exempt.
Looking for a similar assignment? Our writers will offer you original work free from plagiarism. We follow the assignment instructions to the letter and always deliver on time. Be assured of a quality paper that will raise your grade. Order now and Get a 15% Discount! Use Coupon Code "Newclient"
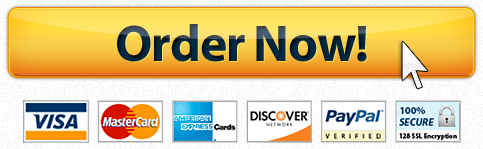